
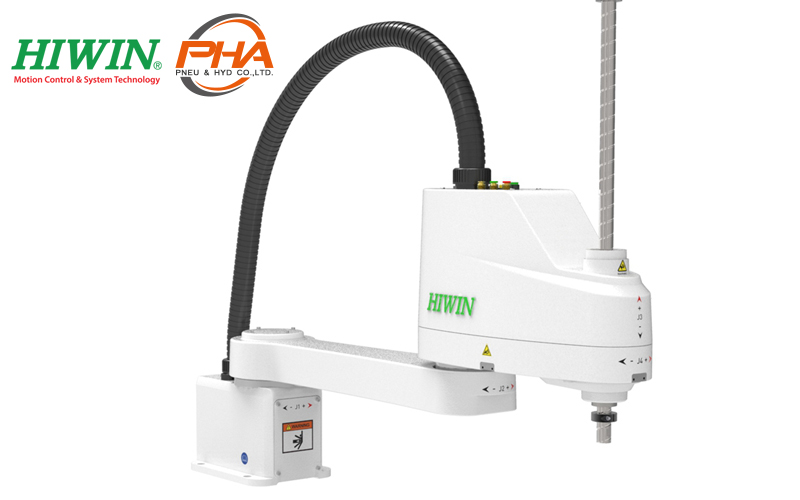
That payload exceeds the capabilities of all but the largest SCARA or six-axis robots. Consider a machining center that makes bearing assemblies of 100 kg or more. What limits SCARA and six-axis robots is that they support loads on extended arms. A robot’s load capacity (defined by the manufacturer) must exceed the total weight of the payload, including any tooling, at the end of the robot arm. That starts with profiling the job’s load, orientation, speed, travel, precision, environment and duty cycle, sometimes called LOSTPED parameters.ġ. To pick a robot, first evaluate the application’s needs.
Scara robot working pdf software#
Programming their movements in 3D is complex, so software typically maps the motion to a set of world coordinates in which the origin sits on the pedestal’s first joint axis. Six-axis robots often execute welding, palletizing, and machine tending. The additional range of movement also lets six-axis robots service a larger volume than SCARAs can. This is suitable for complex movements that simulate a human arm - reaching under something to grab a part and place it on a conveyor, for example. Six-axis robots move forward and back, up and down, and can yaw, pitch, and roll to offer more directional control than SCARAs.
Scara robot working pdf code#
With such designs, OEMs can design controls and mechanical components separately and then tie them together with custom code for a timer to trigger a pick-and-place motion. This Cartesian robot consists of basic system building blocks that were customized later. However, the arm is essentially a lever, and that limits SCARAs’ reach: The joints are load points that need robust bearings and high-torque motors to handle the loads when the arm extends. This makes SCARAs good for vertical assembly operations, such as inserting pins in holes without binding. SCARAs move in the X, Y, and Z planes like Cartesians, but incorporate a theta axis at the end of the Z plane to rotate the end-of-arm tooling. In contrast, SCARAs and six-axis robots typically mount on a pedestal. This file type includes high resolution graphics and schematics when applicable. Cartesian-robot movements stay within the framework’s confines, but the framework can be mounted horizontally or vertically, or even overhead in certain gantry configurations. In contrast, other applications, such as picking bottles off a conveyor, require less precision, so the framework only needs to support the base axis in compliance with the actuator’s manufacturer recommendations.
Scara robot working pdf full#
Certain applications, such as machining tightly toleranced parts, require full support of the base axis, usually the X axis. Physical scaffolding forms a framework that anchors and supports the axes and payload. They make linear movements in three axes, X, Y, and Z. Robots of all types are spreading to new and creative applications, but Cartesian robots in particular are proliferating thanks to linear servomotors, modules, standardized components, and operator-friendly controls that lower cost and boost performance.Ĭartesian robots, sometimes called gantry robots, are mechatronic devices that use motors and linear actuators to position a tool. Therefore, a cost-effective Cartesian robot makes the most sense. The picker must extend a full meter to grab the boxes and move them down to the floor and onto a pallet, making for a cantilever situation. This packaging design uses a robot that picks boxes off a high-speed conveyor and places them on a pallet. And in some cases, online tools let end users and OEMs quickly choose and configure robot features. Advanced controls make the robots user-friendlier than ever, with fewer backend-programming requirements. They automate tasks to accelerate cycle times, increase throughput, and eliminate bottlenecks. The use of Cartesian and six-axis robots, as well as selective-compliance-articulated robot arms (SCARAs) is on the rise.
